15 Common Protections of Refrigeration Equipment
2024-07-30
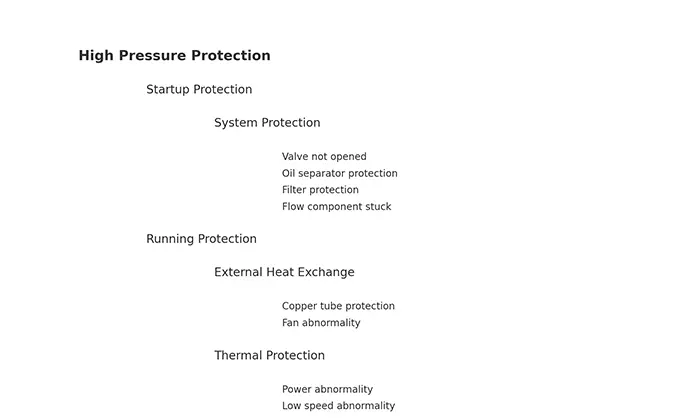
- High Pressure Protection
High pressure protection is to detect whether the refrigerant pressure in the system is normal. When the pressure exceeds the allowable range, the pressure switch acts and transmits the abnormal signal to the high pressure controller. After processing, the refrigeration system's operation will be stopped and the fault will be displayed. - Low Pressure Protection
Low pressure protection detects the return gas pressure in the system and its function is to prevent the compressor from being damaged due to too low system pressure or operation without refrigerant. If the system leaks and there is no refrigerant, forced operation will damage the compressor. At this time, low pressure protection can respond promptly, the control system stops and displays the fault to protect the compressor and the refrigeration system. - Oil Pressure Protection
It is a device to prevent the bearings or other internal components of the compressor from being damaged due to too low lubricating oil pressure. If the amount of compressor oil decreases or the oil supply is cut off, the high-speed running compressor will be severely damaged. The oil pressure protection device is an important component to ensure the safe operation of the compressor. - Anti-freezing Protection:
If the evaporator is too dirty or frosted too severely, the cold air cannot fully exchange heat with the outside hot air, causing the internal unit to freeze. The indoor anti-freezing protection is to stop the compressor before the internal unit freezes to protect the compressor. - Overheat Protection
A well-designed motor operating under specified conditions will not have an internal temperature exceeding the allowable value. However, when the motor operates at too high or too low voltage, or in a high-temperature environment, the internal temperature of the motor exceeds the allowable value. During frequent startups, the temperature will be even higher due to excessive starting current. - High Temperature Protection
Excessive exhaust temperature leads to the decomposition of the refrigerant, aging of the insulating material, carbonization of the lubricating oil, damage to the gas valve, and also clogging of the capillary and the drying filter. The protection method is mainly to sense the exhaust temperature with a temperature controller. The temperature controller should be placed close to the exhaust port. When the exhaust temperature is too high, the temperature controller acts and cuts off the circuit. - Oil Temperature Protection
To prevent the lubricating oil temperature from being too high. During the operation of the compressor, sometimes although the oil pressure difference is normal, the lubrication performance may decrease due to too high oil temperature, resulting in the burning of friction components such as bearing shells. Therefore, the oil temperature protection needs to be controlled. - Cooling Water Cut-off Protection
If the cooling water for the compressor water jacket is cut off, it will cause the exhaust temperature of the compressor to rise, and in severe cases, the cylinder will deform. A pair of electrical contacts are installed on the outlet pipeline of the compressor cooling water jacket. When there is water flowing, the electrical contacts are conducted by water, and the relay sends a signal to enable the compressor to be in a startable or normal operating state. If the water flow is interrupted, the relay electrical contacts are disconnected and the compressor cannot start or stops due to an accident. However, there are often bubbles in the water flow, which may cause false actions, and the water cut-off of the water jacket will not immediately cause an accident. Therefore, the relay should be delayed to act, and the delay is generally 15 - 30 seconds. - Casing Temperature Protection
The casing temperature will affect the life of the compressor. Excessive casing temperature may be caused by insufficient heat exchange capacity of the condenser. Therefore, the air volume or water volume of the condenser, and whether the water temperature is appropriate should be checked. If air or other non-condensable gases are mixed in the refrigeration system, the condensing pressure will rise and the casing will overheat; if the suction temperature is too high, the casing is prone to overheating. In addition, overheating of the motor will also cause the casing to overheat. - Current Protection
When a short circuit occurs in the line, one of the important features is that the current in the line increases sharply. Therefore, it is necessary to set up a corresponding protection device that acts in response to the increase in current when the current flows through a predetermined value, which is called overcurrent protection. - Overheat Protection
A well-designed motor operating under specified conditions will not have an internal temperature exceeding the allowable value. However, when the motor operates at too high or too low voltage, or in a high-temperature environment, the internal temperature of the motor exceeds the allowable value. During frequent startups, the temperature will be even higher due to excessive starting current. - Delayed Start Protection
During the operation of the air conditioner, the compressor may stop running for various reasons. At this time, the high and low pressures in the system will not be balanced immediately. If the compressor is started at this time, it may cause excessive starting current due to pressure problems and burn the air conditioner. Therefore, the current air conditioners are all equipped with delayed start protection, that is, after each stop of the compressor, a delay of 3 - 5 minutes is required before it can be restarted. - Phase Sequence Protection
Phase sequence protection is a protection relay that can automatically identify the phase sequence to avoid accidents or equipment damage caused by the reverse rotation of the motor due to the reverse connection of the power phase sequence of some refrigeration compressors (the sequence of the three live wires is reversed). For example, the structures of scroll compressors and piston compressors are different. Due to the inversion of the three-phase power supply, the inversion of the compressor will be caused, so the inversion is not allowed. Therefore, it is necessary to install a reverse phase protector to prevent the reverse rotation of the chiller. When the reverse phase protector is installed, the compressor can work in the positive phase. When the opposite phase occurs, it is necessary to change two lines of the power supply to the positive phase. - Phase-to-Phase Unbalance Protection
Phase-to-phase unbalanced voltage will lead to three-phase unbalanced current, resulting in a greater temperature rise - set the overload relay. In the maximum phase of the current - Voltage Protection:
The more common shutdown is in the air conditioning system, which is equipped with an overvoltage and undervoltage protection board, and can also achieve phase loss protection. After protection, the corresponding light-emitting diode is lit.
Related Articles
- Have You Encountered the Three Common Problems of Refrigeration Compressors?
- How to Calculate Refrigeration Load? And What Are the Issues?
- What to Do if the Compressor of a Frozen and Refrigerated Display Cabinet Runs but the Refrigeration Effect Is Poor?
- Instructions for Welding and Drainage in the Installation of Refrigeration Equipment Pipelines
- Common Pressure Valves and Protection Devices in Refrigeration Units
- Precautions for Using Rotary Refrigeration Compressors
- What Misconceptions Should Be Avoided in Low - temperature Refrigeration System Repairs
- Essential for Maintenance! Parameters and Phenomena of Normal Operation of Refrigeration and Heating Systems
- Composition and Common Faults of Screw Refrigeration Compressors
- How to Read the High - and Low - Pressure Gauges of Refrigeration Air - conditioners?
- What is Cascade Refrigeration?
- Introduction to Control Valves in Refrigeration Systems
- Welding Equipment Used in Refrigeration System Maintenance
- Where Lie the Key Construction Technologies of the Ammonia Refrigeration System?
- What to Do When a Refrigeration Unit Malfunctions?
- Could a Tiny Copper Tube Cause a Multi - split Air Conditioner to Stop Cooling? Refrigeration Workers Must Pay Attention!
- Has Your Refrigeration System Experienced "Oil Carry - over"?
- Basic Knowledge of Valve - type Components in Refrigeration Systems (Technical Sharing)